Top 5 Reasons: To Use BIM Coordination on Projects
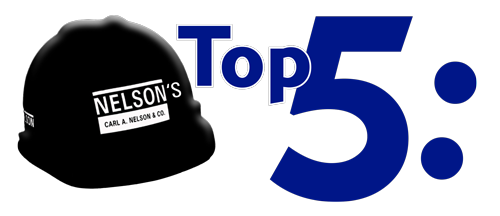
Building Information Modeling (BIM) can offer tremendous benefits on complex construction projects
Here are the Top 5 Reasons you should use BIM coordination on your future building projects.
1: Accelerated Construction Timeframes through Sequencing, Scheduling
Three-dimensional modeling with BIM enables construction schedules to be accelerated by improving efficiency in sequencing of equipment installation and building erection.
Example: On a backup and auxiliary power project for the University of Iowa, where Carl A. Nelson & Company was the general contractor, use of BIM enabled our project team to speed up construction to meet a tight project schedule by identifying the need for placement of temporary and permanent piping supports. On another project for the University of Iowa, construction of a new Biomedical Research Support Facility where CANCO was the design-builder, spatial coordination using BIM allowed for plumbing, mechanical and electrical components to be laid out in pipe racks and installed prior to interior wall construction. This shaved months from the construction schedule.
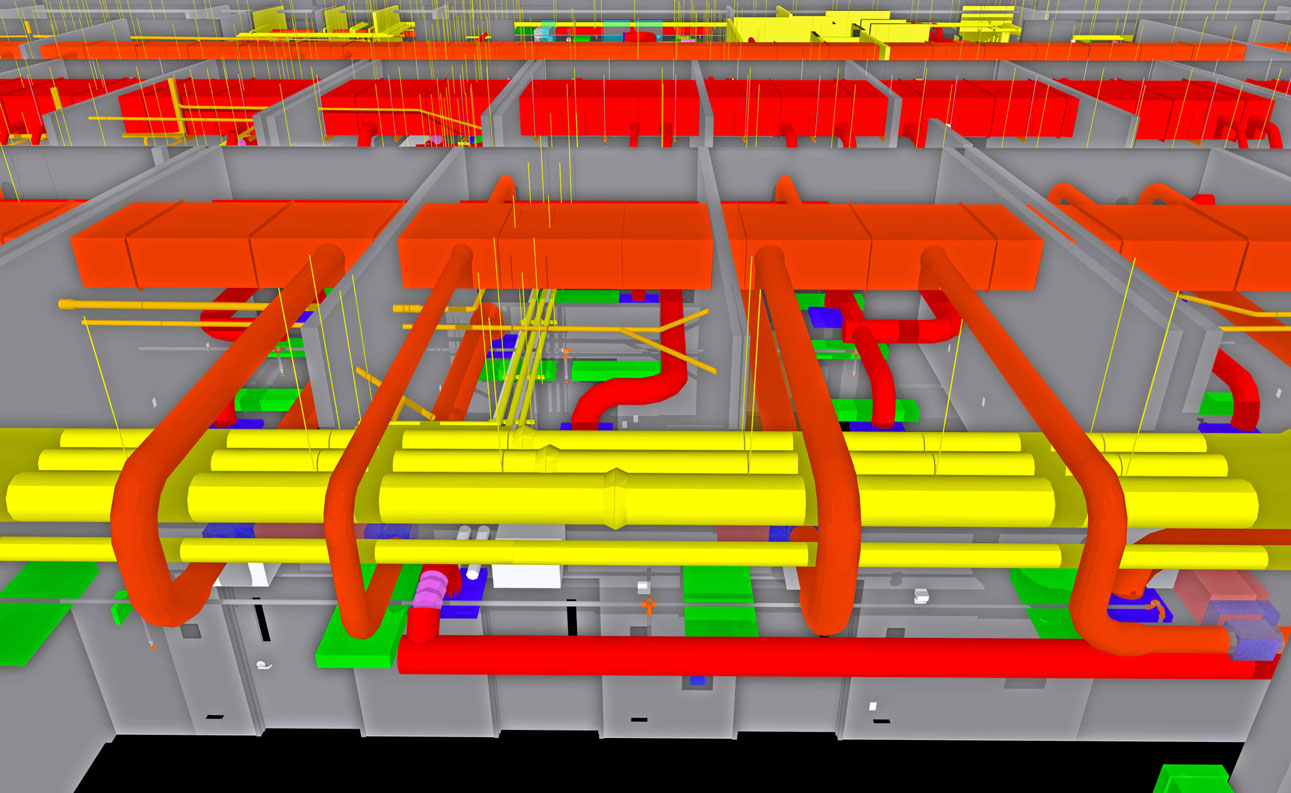
2: Clash Detection to Prevent Rework, Delays in the Field
When spaces are tight, the accuracy afforded by BIM coordination can be invaluable in ensuring items will fit where they are intended to go.
Example: On a project for the University of Iowa during the fit-out of a new Vivarium Space and lab remodeling in a sub-basement of the Pappajohn Biomedical Discovery Building, BIM coordination identified multiple MEPT and structural clashes in the head space above the ceiling, where space was at a premium. Many clashes were avoided, but in some areas, the model showed it would be necessary to lower ceiling heights to create adequate room above the ceiling. Beyond clash detection between systems and structure, BIM also helps ensure ease of installation of production or process equipment. While working for an agricultural client in the Midwest, the Carl A. Nelson & Company team used BIM to identify a conflict where the design would have prevented installation of a large piece of equipment had the structure been previously completed.
By identifying these issues in advance of construction, rework that would have resulted in extra cost and schedule delays was avoided.
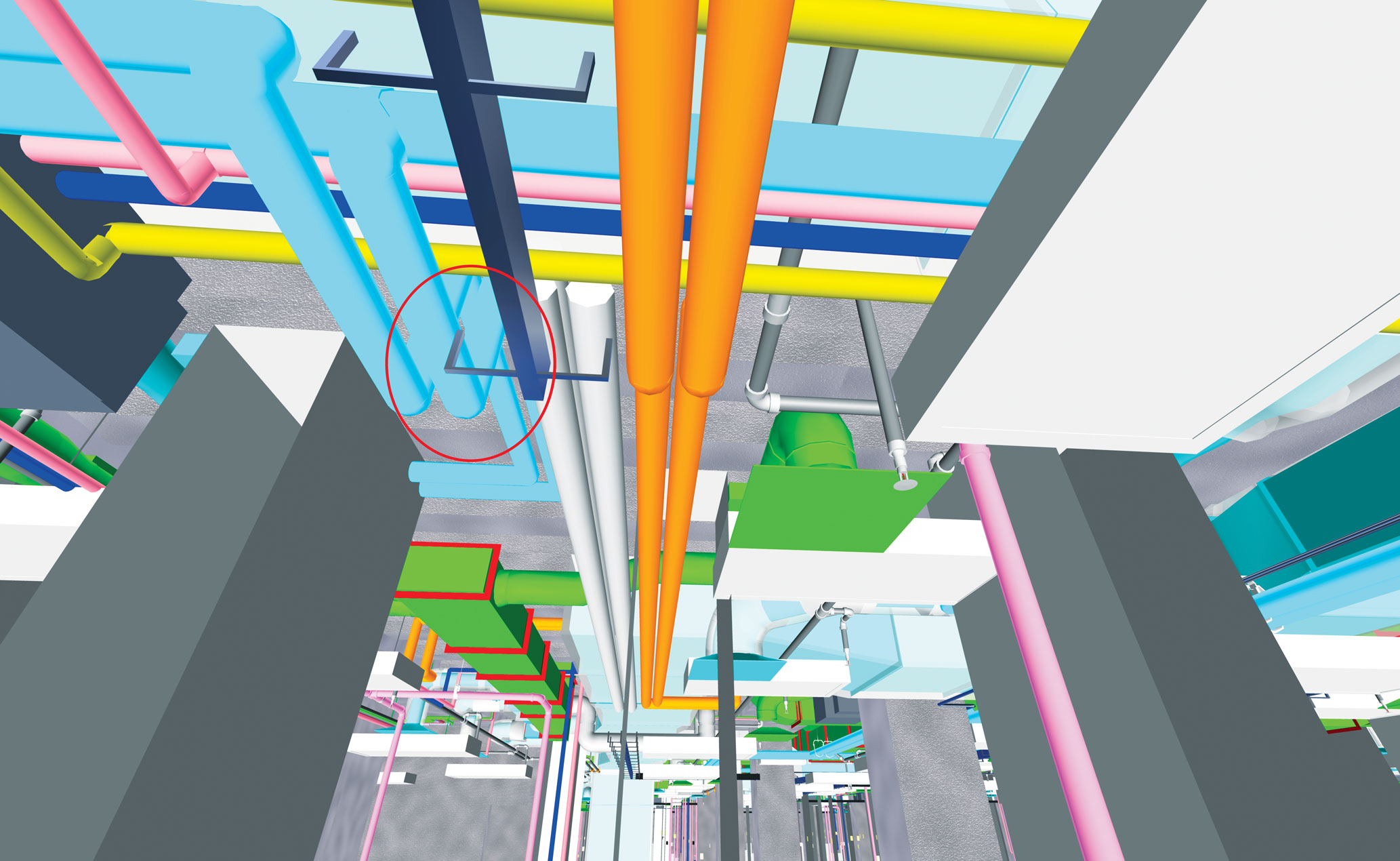
3: Clarity for Field Personnel during Construction Phase
When a project involves complex installations and erection, BIM enables activities to be planned for greatest efficiency by identifying potential conflicts in advance of construction.
Example: For a seed and grain industry client in Indiana, Carl A. Nelson & Company's use of BIM eased construction of a new structure being built with existing buildings on two sides and existing pipe racks and electrical substations on a third. The BIM was used to properly position cranes for complicated lifts of both structure and equipment. The model gave CANCO field personnel the ability to proceed with building erection while waiting for delivery of an evaporator, and aided in sequencing the installation of structural steel. Use of BIM also provides a tool for helping field personnel to visualize and understand the sequencing plan.
4: Accuracy of Material, Equipment Installation through Prefabrication
BIM coordination from design and subcontractor drawings allows for on- or off-site prefabrication of materials, which speeds the project schedule while also ensuring equipment will fit when installed.
Examples: Off-site prefabrication of high-pressure steam and condensate piping for the University of Iowa Power Plant; shop fabrication of new piping for an industrial client in southeast Iowa where CANCO was general contractor after a change order enabled our team to perform 3D scans of existing piping and to create new 3D models; and off-site cutting of glazed concrete masonry and pre-installation of boxes for electrical and mechanical wall devices that improved contamination prevention in the University of Iowa's Biomedical Research Support Facility.

5: Improved Planning, Execution of Ongoing Facility Maintenance
Use of BIM helps with future maintenance and ease of use of completed facilities by giving maintenance staff and end-users the chance to see the facility in 3D before it is built, in order to have input on changes that could improve operating efficiency.
Example: On a project for an industrial client, the Carl A. Nelson & Company project team identified locations of above-ceiling variable air volume (VAV) boxes that were part of the HVAC system, which must be accessed for testing, balancing, cleaning and future replacement. Using BIM, it was possible to ensure access to the VAV boxes was not impeded by installation above or adjacent to lighting, fire sprinklers, mechanical piping and electrical cable trays. The model also helps the Owner to identify the locations of the boxes for maintenance.
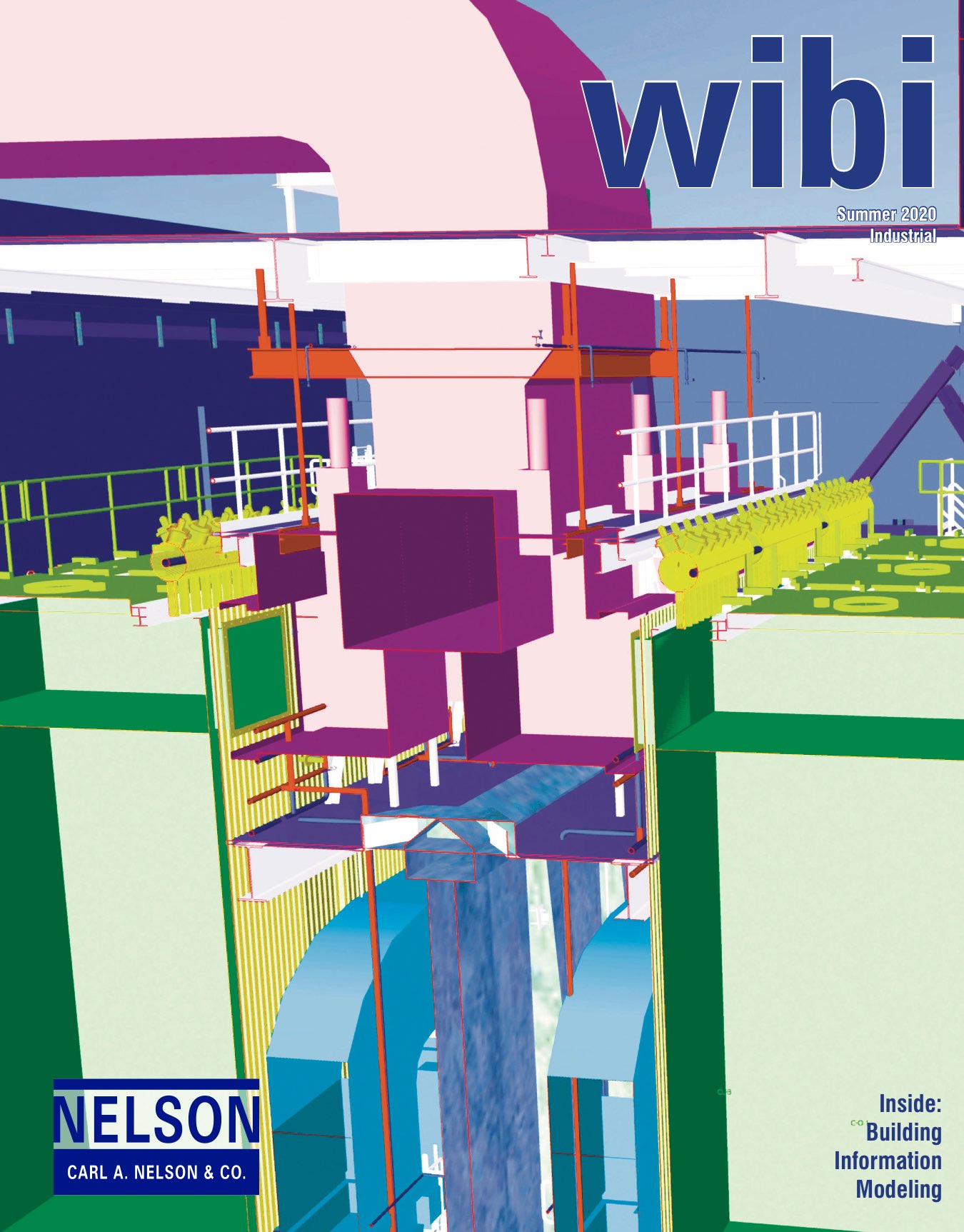
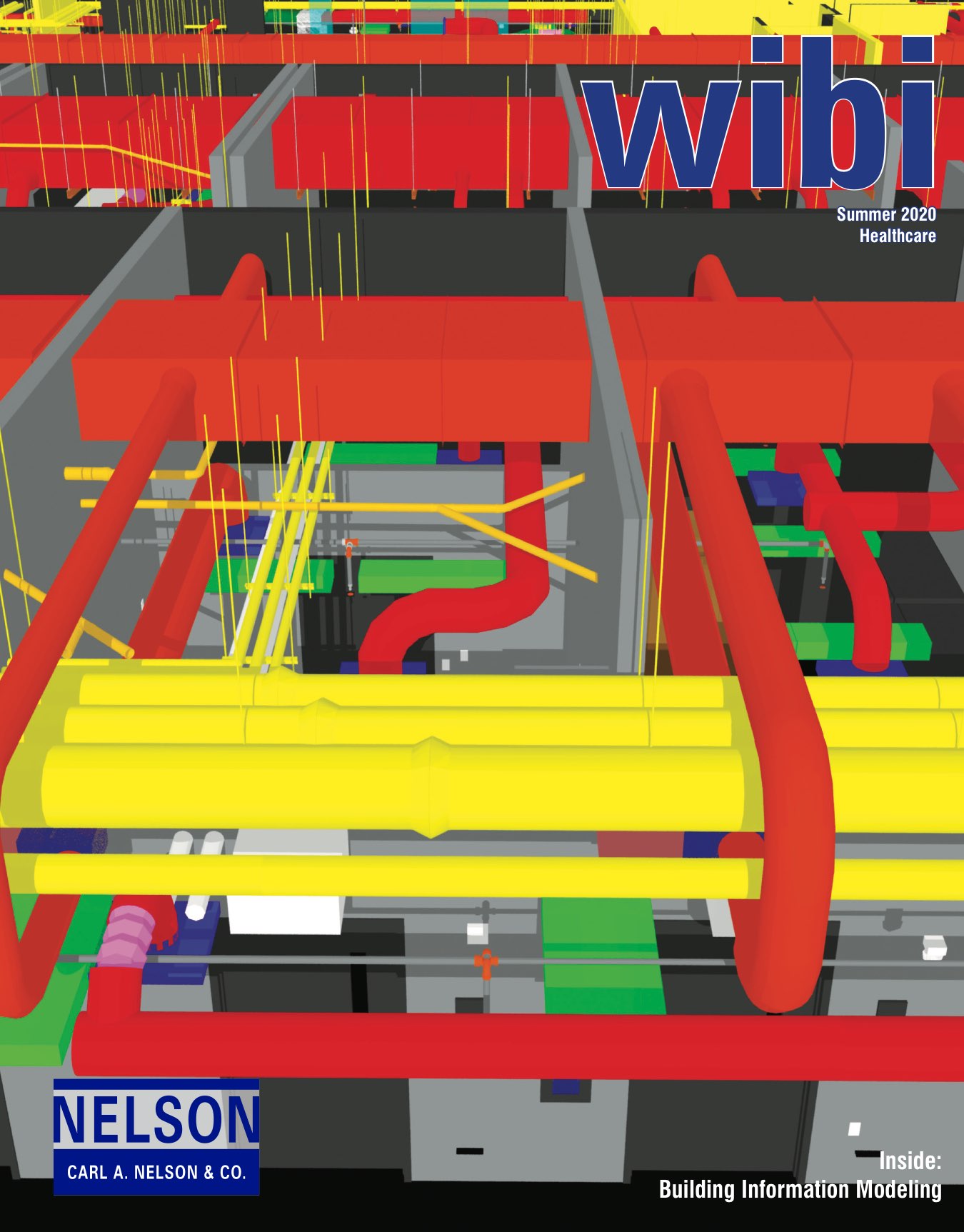
Build it Better with BIM
You can get additional details, and perspectives from our design and construction professions, about Building Information Modeling and its benefits for complex construction projects in healthcare and industrial facilities by turning to our wibi newsletter.