Thermal barriers for spray-foam insulation
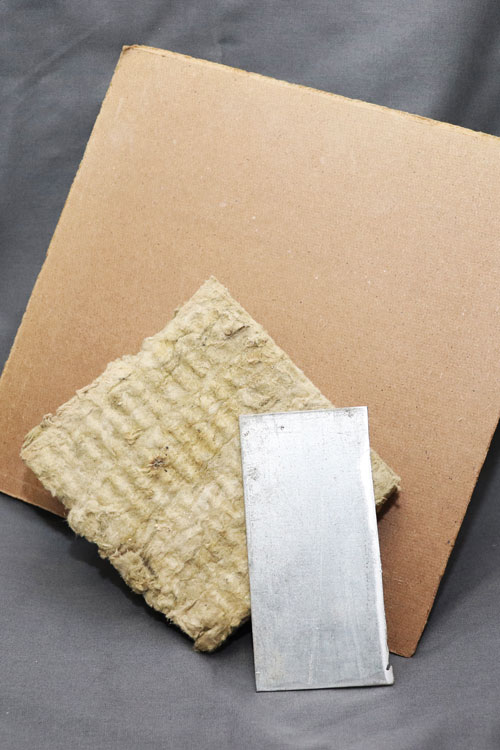
3 years, 5 months ago
We frequently encounter building interiors in factories or warehouses with exposed spray foam insulation. In most instances, the International Building Code (IBC) requires a thermal barrier between the plastic and occupied spaces. This article summarizes when a thermal barrier is required, which is specified in Section 2603.4.
Thermal Barrier Required:
Foam plastic shall be separated from the interior of a building with an approved thermal barrier. The thermal barrier may be ½” gypsum board, or a material that is tested in accordance with and meets the acceptance criteria of NFPA 275 Temperature Transmission Fire Test and the Integrity Fire Test. The purpose of the thermal barrier is to limit the temperature rise of the foam plastic.
Exceptions:
Several exceptions to the aforementioned requirement are delineated in the IBC. The first is combustible concealed spaces shall comply with Section 718. Section 2603.4.1 also lists several additional exceptions, the most pertinent are summarized below. Please refer to the code section for a full listing of requirements.
- Masonry or concrete construction - where the foam plastic is covered on each face by a minimum of one inch of masonry or concrete construction in the wall, floor, or roof system.
- Cooler and freezer walls – maximum of ten inches thick and needs to meet the requirements of 2603.4.1.3
- Walk-in coolers
- Exterior walls of one story sprinklered buildings where the foam plastic is covered by a minimum of 0.032 inch thick aluminum or 0.0160 inch thick corrosion-resistant steel.
- Roofing – Foam insulation part of a Class A, B, or C roofing assembly. The plastic must be covered by not less than 0.47 inch wood structural panel sheathing or pass the testing requirements of NFPA 276 or UL 1256.
- Attics or crawl spaces where entry is only to service utilities may be separated by an ignition barrier in lieu of a thermal barrier. The materials below may be used as an ignition barrier.
- Mineral Fiber Insulation 1 ½” thick
- Wood structural panels ¼” thick
- Particleboard ¼” thick
- Hardboard ¼” thick
- Gypsum board 3/8” thick
- Corrosion-resistant steel having a base metal thickness of 0.016”
- In attic spaces only: self-supported spray applied cellulose insulation 1 ½” thick
An additional exception to the requirement for thermal barriers is found in section 2603.9 and is based on special approval after passing large scale tests such as NFPA 286, FM 4880, UL 1040, and UL 1715. The testing is based on the actual configuration of the foam plastic assembly and must be tested in the maximum thickness and density intended for use. The tested assemblies must include typical seams, joints, and other details that will occur in the installation. This exception is commonly used for composite foam insulated metal panels.
Two methods are available in order to demonstrate compliance with 2603.9. The first is to provide the test report that contains the description of the assembly and verifies the foam plastic in the end-use application passes the test. The second is to obtain an evaluation report from a testing agency such as ICC-ES that covers the end-use application.
As is probably evident from reading this article, meeting the requirements of the IBC when using foam plastics in your building is complicated. If you have questions or need assistance, please contact me.
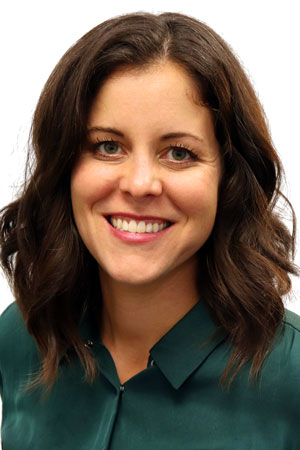
About the Author
Ellen McCulley graduated magna cum laude with a Bachelor of Architecture degree from Iowa State University, where she received the Pella Architectural Award from the Department of Architecture in the College of Design. She is a registered architect in Iowa, Illinois, Nebraska and Missouri, and joined Nelson Design, Inc., a wholly owned subsidiary of Carl A. Nelson & Company, in 2012.
How to obtain code review for your project or facility
Carl A. Nelson & Company is available to help clients address code-related issues in their facilities. Call (319) 754-8415 and ask for Ellen McCulley. Review past installments of Decoding the Code at www.carlanelsoncoconstruction.com/decoding-the-code/